How much electricity does a 3D printer use? This question is increasingly relevant as 3D printing gains popularity. Understanding the energy consumption of these machines is crucial, not only for managing electricity costs but also for making informed decisions about sustainable manufacturing practices. This exploration delves into the various factors influencing a 3D printer’s power draw, from printer size and printing technology to the phases of the printing process itself.
We’ll provide a clear picture of how much energy you’re using and offer tips to minimize your environmental impact.
From the wattage of different models to the impact of ambient temperature, we’ll break down the complexities of 3D printing energy consumption. We’ll equip you with the knowledge to calculate your electricity costs, monitor usage, and implement energy-saving strategies. Whether you’re a seasoned 3D printing enthusiast or a curious beginner, this guide will provide valuable insights into the energy efficiency of your 3D printing endeavors.
Power Consumption Factors in 3D Printing

The energy consumption of a 3D printer is a multifaceted issue, influenced by a variety of factors beyond simply the printer’s model. Understanding these factors is crucial for both responsible energy usage and informed purchasing decisions. This section will delve into the key elements that determine a 3D printer’s power draw.
Printer Size and Electricity Usage, How much electricity does a 3d printer use
Generally, larger 3D printers consume more electricity than smaller ones. This is primarily due to the increased mass of the heated components (nozzle, bed) requiring more energy to reach and maintain operating temperatures. Larger build volumes also often necessitate more powerful heating elements and potentially more powerful fans for cooling. For example, a large-format industrial printer with a substantial heated build chamber will have significantly higher power consumption than a small desktop FDM printer.
The increased surface area of the build plate in larger printers also contributes to heat loss, requiring more energy to compensate.
Impact of Different 3D Printing Technologies
Different 3D printing technologies exhibit vastly different energy consumption profiles. Fused Deposition Modeling (FDM) printers, the most common type, generally have moderate energy consumption, primarily driven by the heating of the nozzle and bed. Stereolithography (SLA) and Selective Laser Sintering (SLS) printers, on the other hand, often have higher energy demands. SLA printers require powerful UV lasers and precise temperature control, leading to increased electricity usage.
SLS printers, which use a high-powered laser to melt and fuse powder materials, are among the most energy-intensive 3D printing technologies. Material Jetting (MJF) technologies also typically require significant energy for the heating and curing processes. The specific energy consumption depends on the laser power, build chamber size, and the material used.
Electricity Consumption During Different Printing Phases
The power consumption of a 3D printer varies considerably across different phases of the printing process. The heating phase, where the nozzle and build plate are brought to their operating temperatures, typically constitutes a significant portion of the total energy usage. This initial heating phase consumes the most energy. The printing phase itself consumes a moderate amount of energy, with the power draw fluctuating depending on the printing speed, material being used, and the complexity of the model.
Finally, the cooling phase, while generally less energy-intensive than heating, still contributes to the overall energy consumption. The duration of each phase significantly impacts the overall energy used for a single print job.
Comparison of Power Consumption Across Popular 3D Printer Models
Model | Technology | Wattage | Estimated kWh per hour of printing |
---|---|---|---|
Creality Ender 3 V2 | FDM | ~35W (average) | ~0.035 kWh |
Prusa i3 MK3S+ | FDM | ~40W (average) | ~0.040 kWh |
Formlabs Form 3 | SLA | ~100W (average) | ~0.1 kWh |
HP Jet Fusion 5200 | MJF | Variable, High | Variable, High (several kWh) |
Note
Wattage and kWh estimates are approximate and can vary based on usage and specific model variations. The HP Jet Fusion 5200 is included to illustrate the significant difference in power consumption between desktop and industrial-scale printers. Actual power draw can be significantly higher due to the high-power laser and the large build chamber.
Estimating Electricity Costs for 3D Printing: How Much Electricity Does A 3d Printer Use

Accurately estimating the electricity consumption and associated costs of 3D printing is crucial for budgeting and optimizing printing processes. Understanding the factors influencing energy usage allows for more informed decisions regarding print parameters and printer selection. This section will provide a framework for calculating electricity costs and methods for monitoring energy consumption.
Calculating the precise cost of electricity used by a 3D printer requires considering several factors. A fundamental formula provides a starting point, but real-world applications necessitate a more nuanced approach.
Electricity Cost Calculation Formula
The basic formula for calculating the electricity cost of a 3D printing project is straightforward:
Total Cost = (Wattage × Hours × Price per kWh) / 1000
Where:* Wattage: The power consumption of the 3D printer in watts (W). This information is typically found in the printer’s specifications.
Hours
The total printing time in hours.
Price per kWh
The cost of electricity per kilowatt-hour (kWh) from your electricity bill.This formula provides a reasonable estimate, but it simplifies the complex energy dynamics of 3D printing.
Ever wondered how much juice your 3D printer guzzles? It varies wildly depending on the model and print size, but think of it like this: the energy used is roughly equivalent to powering a small lamp. While you’re calculating that, check out this awesome a cold wall mens brutalist print cotton – it’s got a similarly striking geometric design! Back to the power draw, though – smaller prints naturally consume less electricity than marathon printing sessions.
Factors Influencing Actual Electricity Cost
Several factors can significantly influence the actual electricity cost beyond the basic formula. These factors introduce variability and necessitate a more comprehensive approach to cost estimation.
One key factor is idle time. 3D printers often consume power even when not actively printing, particularly if they maintain a heated bed or nozzle. This idle power consumption contributes to the overall energy usage. The longer the idle time, the higher the electricity cost. For example, a printer with a 100W heated bed left on for 8 hours overnight will consume 800 Wh (0.8 kWh) even without any active printing.
Ambient temperature also affects energy consumption. In colder environments, the printer might require more energy to maintain the desired bed and nozzle temperatures, leading to increased electricity usage. Conversely, in warmer environments, less energy might be needed. This variability highlights the importance of considering environmental conditions when estimating costs. For instance, printing in a cold garage might increase energy consumption by 20-30% compared to a climate-controlled room.
Monitoring and Tracking Energy Usage
Precise monitoring of a 3D printer’s energy usage requires specialized equipment.
One method involves using a kilowatt-hour (kWh) meter. These devices plug between the printer’s power cord and the wall outlet, providing a real-time display of power consumption in watts and accumulated energy usage in kWh. This allows for direct measurement of energy usage during both printing and idle periods. Regular readings provide data to refine cost estimations. For instance, a kWh meter can record the energy used for a specific print job, providing a more accurate cost calculation than the simplified formula.
Another approach is to use a smart plug. Many smart plugs offer energy monitoring features, providing data on power consumption through a mobile app. This data can be logged and analyzed over time to create a detailed picture of the printer’s energy usage patterns. The app often provides graphs and summaries of daily or weekly energy consumption, facilitating easy tracking and analysis.
Estimating Total Electricity Cost for a Specific Project
Let’s illustrate estimating the total electricity cost for a specific project.
Assume a 3D printer with a rated power consumption of 200W (this includes the heated bed and extruder) is used to print a model for 5 hours. The electricity price is $0.15 per kWh. Using the formula:
Total Cost = (200W × 5 hours × $0.15/kWh) / 1000 = $0.15
This calculation, however, doesn’t account for idle time. If the printer was left on for an additional 2 hours with a standby power consumption of 50W, the additional cost would be:
Additional Cost = (50W × 2 hours × $0.15/kWh) / 1000 = $0.015
Therefore, the total estimated cost, including idle time, would be $0.15 + $0.015 = $0.165. This example demonstrates that even seemingly small idle power consumption can significantly impact the overall electricity cost over time. More sophisticated monitoring techniques, as discussed above, would yield even more accurate estimates.
Energy Efficiency Tips for 3D Printing
Reducing the energy consumption of 3D printers is crucial for both environmental responsibility and cost savings. While 3D printing offers significant advantages in design and manufacturing, its energy footprint should not be overlooked. By implementing several strategies, users can significantly minimize energy usage without compromising print quality or functionality. This section details practical methods for achieving energy efficiency in 3D printing.
Methods to Reduce Energy Consumption
Optimizing energy use in 3D printing involves a multifaceted approach encompassing hardware, software, and material choices. Improving energy efficiency begins with selecting an energy-efficient printer model, characterized by lower power consumption ratings. Regular maintenance, such as keeping the printer’s cooling system clean and unobstructed, also plays a vital role in reducing energy waste. Furthermore, turning off the printer completely when not in use, rather than leaving it in standby mode, significantly reduces energy consumption over time.
Finally, strategically scheduling print jobs during off-peak hours can leverage lower electricity rates, offering both environmental and financial benefits.
Optimizing 3D Printing Settings for Energy Efficiency
Careful adjustment of 3D printing settings offers substantial potential for energy savings without sacrificing print quality. Reducing print speed can lower the energy demand, although this will increase print time. However, this trade-off can be beneficial, particularly for long prints, where the overall energy consumption might be lower despite the increased duration. Similarly, optimizing infill density can reduce material usage and thus the energy required for extrusion.
A lower infill density, while potentially affecting structural integrity depending on the application, generally reduces material usage and, consequently, energy consumption. Experimentation and fine-tuning are crucial to finding the optimal balance between print quality and energy efficiency. For instance, a 20% infill might suffice for a non-load-bearing model, while a denser infill is necessary for functional parts.
Energy Efficiency of Different Filament Materials
The type of filament used significantly impacts energy consumption. PLA (polylactic acid), a bioplastic derived from renewable resources, generally requires less energy to melt and extrude compared to ABS (acrylonitrile butadiene styrene). ABS, known for its higher strength and heat resistance, demands higher temperatures during printing, resulting in increased energy usage. Therefore, choosing PLA for projects where its properties are suitable can contribute to considerable energy savings.
Other materials, such as PETG (polyethylene terephthalate glycol-modified), offer a balance between properties and energy efficiency, making it a viable alternative depending on the specific application. For example, a comparison of energy consumption during a 10-hour print using PLA versus ABS might show a noticeable difference, highlighting the energy-saving potential of material selection.
Best Practices for Responsible and Energy-Conscious 3D Printing
Implementing several best practices can collectively promote energy-conscious 3D printing.
- Prioritize print design for minimal material usage. This includes optimizing the model’s geometry to reduce unnecessary volume and weight.
- Utilize energy-efficient printer models with features like automatic shut-off and sleep modes.
- Regularly maintain the printer to ensure optimal performance and minimize energy waste.
- Employ energy-saving settings within the slicer software to fine-tune print parameters for efficiency.
- Choose filament materials with lower energy requirements, such as PLA, when appropriate for the project.
- Schedule print jobs during off-peak hours to take advantage of lower electricity rates.
- Consider the environmental impact of filament production and disposal when selecting materials.
Wrap-Up

Ultimately, understanding how much electricity your 3D printer consumes empowers you to make informed choices. By considering the factors discussed – printer size, technology, printing time, and energy-saving techniques – you can optimize your printing process for both cost-effectiveness and environmental responsibility. Remember, responsible 3D printing isn’t just about creating amazing designs; it’s also about minimizing your environmental footprint.
By being mindful of energy consumption, you can contribute to a more sustainable future for additive manufacturing.
Question & Answer Hub
What factors affect 3D printer electricity usage besides the printer’s wattage?
Ambient temperature, filament type, print speed, and the complexity of the print all influence energy consumption. Higher temperatures and complex prints generally require more energy.
Can I use a power meter to track my 3D printer’s energy use?
Yes, a simple energy meter plugged between the printer and the wall outlet can accurately measure your 3D printer’s energy consumption in kilowatt-hours (kWh).
Are there energy-efficient filament materials?
While the filament material itself doesn’t directly impact energy consumption significantly, using less filament through optimized designs can indirectly reduce energy usage.
How often should I calibrate my 3D printer to improve energy efficiency?
Regular calibration (as recommended by the manufacturer) ensures optimal performance, which can indirectly lead to more efficient energy use by preventing wasted prints due to malfunctions.
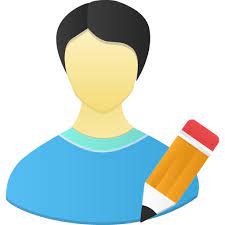
Printer Review is a website that provides comprehensive and insightful information about various types of printers available in the market. With a team of experienced writers and experts in the field, Printer Review aims to assist consumers in making informed decisions when purchasing printers for personal or professional use.